Safety training in the automotive industry

Executive Summary: The automotive industry presents various hazards. This makes effective safety training crucial. This blog highlights the importance of comprehensive training programs. It emphasizes the benefits of using microlearning to supplement traditional methods. Discover how microlearning promotes a safer working environment in the automotive sector.
In the automotive industry, factory floors are bustling hubs of activity. Man and machine function in tandem to produce vehicles. With a multitude of moving machinery and a large workforce, there is always a risk of accidents or serious injuries. That makes it essential to prioritize safety training and the well-being of employees.
The US Bureau of Labor and Statistics (BLS) consistently ranks the automotive industry among the top 25 most dangerous jobs. |
This industry involves exposure to heavy machinery, toxic chemicals, sharp tools, and various hazardous equipment. A 2018 report by BLS showed that nonfatal injury and illness rates are double in the automotive industry, compared to private industries. This illustrates the high levels of risk in the automotive industry. It’s also why there are significant healthcare and compensation expenses, totaling over $120 million annually.
Safety training plays a pivotal role in the automotive industry. It is an essential means to mitigate risks and hazards. It is important to equip workers with the knowledge and skills to safely navigate the factory environment. This way, accidents and injuries can be significantly reduced. Proper safety training enables employees to identify potential dangers and operate machinery correctly. It also trains them to respond effectively in emergency situations.
One of the “root causes” of workplace injuries, illnesses, and incidents is the failure to identify or recognize hazards that are present, or that could have been anticipated. A critical element of any effective safety and health program is a proactive, ongoing process to identify and assess such hazards (Occupational Safety and Health Administration, 2016). Let’s begin by understanding the hazards in the automotive industry.
People forget nearly 90% of what they have learnt within just 7 days, unless the concepts are reinforced. That’s why employees swamped with documents, presentations, and classroom sessions are not likely to learn much.
However, time constraints make it difficult to reinforce vast concepts.
What can you do instead? Arm your employees with one concept at a time. Studies show the human attention span is only 8.25 seconds, so keep your training concise.
RapL is your software for that.
Hazards in the automotive industry
The International Labour Organization identifies 5 categories of hazards in the automotive industry. These are:
- Accident hazards: Accidents in the workplace can result in injuries when workers operate equipment, handle materials, or transition between stations. Some of these injuries can have long-lasting consequences. This can include permanent disability or even loss of life.
Examples of accident hazards include:- Falling from heights, slipping and tripping on wet or greasy surfaces
- Injuries from collapsing equipment and falling vehicles
- Injuries from being caught between objects
- Injuries caused by rotating machine parts
- Musculoskeletal injuries from lifting heavy parts
- Burns from hot surfaces and chemicals
- Electrocution from faulty equipment or live wires
- Carbon monoxide poisoning
- Fires and explosions from flammable substances
- Increased road accidents during test drives
- Punctures and cuts from sharp tools and materials
- Accidents from bursting of compressed-air lines and tires or improperly-maintained pressure cleaners
- Physical hazards: Physical hazards in the workplace include exposure to high levels of noise or radiation. They also include risks from working in extreme hot or cold temperatures.
Examples of physical hazards include:
- Exposure to ultraviolet and infrared radiation from welding
- Microwave and radiofrequency radiation
- Hand-arm vibration leading to white finger syndrome or carpal tunnel syndrome
- Excessive noise levels (> 90 dBA)
- Extreme heat or cold conditions resulting in fire or carbon monoxide poisoning.
- Chemical hazards: Occupational health hazards include skin diseases and conditions. These can be caused by exposure to chemicals, such as adhesives and oils.
Examples of chemical hazards:
- Eye irritation and respiratory issues from contact with irritating chemicals and their fumes
- Asbestosis and mesothelioma from asbestos dust in brake drum cleaning
- Chronic poisoning from lead exposure
- Hematological changes from solvent exposure
- Increased risk of cancer and organic brain damage from inhaling diesel exhaust fumes and heavy metals, benzene, etc
- Respiratory issues from nitrogen dioxide and particulate inhalation
- Gastrointestinal disturbances from adhesive ingestion
- Injuries from splashes of corrosive chemicals.
- Biological hazards: Biological hazards include infections. These can be caused by microorganism contamination and growth in adhesives. These can also include exposure to mold, bacteria, allergens, etc. from dust and organic materials. Biological hazards can originate from various areas in an automobile factory. These can be manufacturing areas where adhesives are used. Storage areas can also have mold growth. Areas where organic materials are processed or handled can also carry these organisms. These pose risks to the respiratory system and overall health of workers.
- Ergonomic and psychosocial factors: In the automotive industry, workers face the risk of acute musculoskeletal injuries. This can happen due to overexertion and incorrect lifting techniques. Workers can also suffer from cumulative trauma disorders, like carpal tunnel syndrome, from repetitive tasks. Additionally, the intensive and high-pressure nature of the work contributes to psychological stress for employees.
Safety measures in the automotive industry
At a foundational level, automotive companies can implement control measures to mitigate hazards: (Ask-EHS, 2019)
- Provide comprehensive training on proper lifting techniques and manual handling procedures.
- Promote the use of mechanical load-shifting devices. These can include cranes, hoists, hand trucks, forklifts, etc. They can help workers handle difficult loads.
- Ensure the use of personal protective equipment (PPE). Follow machinery guarding guidelines, especially for grinders and similar equipment.
- Implement job rotation strategies. This prevents workers from performing repetitive tasks for extended periods.
- Conduct thorough risk assessments. Also carry out pre-operational inspections before undertaking any tasks.
- Implement a permit-to-work system. This ensures safe and efficient execution of work.
- Install splash guards and conduct written risk assessments. This helps identify and control hazards associated with hazardous substances.
- Develop and implement a regular service regime for equipment and machinery.
- Strictly follow lockout-tag out procedures. This prevents accidents during maintenance or repairs.
- Monitor and control noise levels to comply with national standards (not exceeding 85 dB). Conduct audiometric tests as needed.
- Conduct regular fire evacuation drills.
- Establish a communication system. This ensures workers can contact others in case of emergencies when working alone.
Importance of safety training in the automotive industry
We saw earlier that the automotive industry consistently ranks among the top 25 most dangerous jobs. This highlights the importance of safety training. By reducing risks and promoting a safety-conscious culture, safety training ensures the well-being of employees. This fosters a secure work environment.
- Creating awareness and ensuring employee safety: With the right safety training, companies can increase awareness of potential hazards. They can also educate employees on correct procedures and policies (Chinn, 2019). This way, safety training promotes a healthy work environment. It safeguards the well-being of employees and also reduces healthcare costs.
- Reducing accidents and injuries: Preventing accidents and occupational illnesses is crucial for several reasons. Firstly, it is a moral obligation to protect the health and lives of employees. Secondly, accidents and injuries lead to downtime. This reduces efficiency and productivity. Accidents can also harm a company’s reputation. This affects stakeholder and investor confidence (ResponsAble, 2023).
- Compliance with regulations and legal requirements: Compliance with safety regulations is a legal requirement. Violations can lead to significant financial penalties (as we saw earlier, this can go to approx. $120 million annually). Safety training educates employees on safety protocols and best practices. This ensures operations are conducted in accordance with established standards. This minimizes the risk of violations and potential legal consequences.
- Building a safety culture within the organization: Safety training and culture is a deep and intrinsic part of an organization. It is woven into the cultural fabric of the organization itself. It is a reflection of the organization, why they exist, and how they choose to interact with and impact the world around them (Chandel, 2022). Building a safety culture within the automotive organization goes beyond mere compliance. It involves instilling a mindset where safety is a core value embraced by every individual. This proactive approach empowers employees to prioritize safety. It creates a harmonious work environment dedicated to preventing accidents and promoting employee well-being.
- Enhancing productivity and efficiency: Safety training in the automotive sector not only safeguards employees, but also enhances productivity and efficiency. Well-trained workers are more confident. Thus, they make fewer mistakes. They also follow streamlined processes. This leads to smoother operations and increased output.
Microlearning for safety training
Traditional safety training often overlooks the principles of adult education. It lacks flexibility in terms of schedules and accessibility. It can also be overwhelming. Traditional safety training often involves large chunks of information and long sessions. This can hinder the effectiveness and relevance of safety training. This is because employees may not feel engaged with the training. Therefore, they won’t be able to retain the knowledge required to navigate the workplace safely. To overcome these limitations of traditional training, microlearning can be a viable solution.
Microlearning offers bite-sized, accessible content. This allows flexible and personalized training experiences. This can enhance the effectiveness and relevance of safety training. It contributes to a safer and more informed work environment.
- Scenario-based learning: In safety training, scenario-based learning (SBL) offers an immersive experience. Scenarios simulate real-world situations. Learners face realistic work challenges and receive relevant feedback. The storytelling nature of scenario-based learning intrigues learners’ psychology and curiosity (Learning Everest, 2023). This improves interactivity, skill development, and employee engagement. It creates a dynamic and exciting learning environment. Through experiential learning, scenario-based safety training prepares employees for real-world situations.
- Increased engagement and retention of knowledge: Microlearning is based on Ebbinghaus’ Forgetting Curve. It reveals that people forget over 70% of what they have learned within just 3 days—unless the knowledge is reinforced at spaced intervals. This is known as spaced repetition learning. It is integral to microlearning. Through bite-sized content repeated at regular intervals, microlearning enhances knowledge retention. Spaced repetition ensures that training is more effective, as learners retain knowledge for longer periods and can apply it effectively in their work.
- Real-time tracking: Real-time tracking is vital for effective safety training. It allows L&D managers to easily identify knowledge gaps. This helps them provide targeted training and address specific areas of improvement. This ensures workers gain in-depth and comprehensive knowledge of safety in the automotive workplace. This is crucial for risk reduction and employee safety. Progress tracking and personalized learning experiences enhance safety awareness and adherence. This creates a safer workplace for all employees.
Microlearning is complementary to in-person workplace safety training
To optimize the effectiveness of microlearning in safety training, it is important to understand how to use it correctly. In safety training, microlearning is not a standalone solution. It should be used to supplement, reinforce, and refresh other training techniques. The strength of microlearning lies in just-in-time training. It provides timely and relevant support to learners precisely when they require it (LinkedIn).
Managers often face the challenge of maintaining employees’ attention during safety training. To overcome this, microlearning offers concise and focused content that keeps employees engaged.
“Ideally, microlearning should be on a topic you’ve already learned, but in a different format,” said Dayna Nota, Manager of Training and Development at Magid. “It can be hard to remember things from a training class or conference. It should be a good refresher. You can also use it as pre-work before a training session.”
For example, consider a session on ladder safety training. It includes explanations, slides, and hands-on demonstrations. After a week, this can be supplemented with a link to a short microlearning video on ladder safety reminders. Nota highlights that this allows workers to review the material and refresh the knowledge. It is a great way to leverage spaced repetition and microlearning.
Continuous learning: Updated industry standard-level content
In the automotive industry, there are many advancements and evolving safety regulations. It’s crucial for automotive professionals to stay updated on the latest practices and procedures. However, it can be challenging to keep employees informed of all the latest developments. This is where microlearning can be effective.
Microlearning modules can be easily updated and modified. Content on new regulations, emerging technologies, and best practices can be added quickly and seamlessly. This flexibility ensures that employees are equipped with the most current and relevant knowledge. It enables them to uphold industry standards. They can function safely and with relatively lower risk.
Examples of safety training topics
Examples of safety training topics include:
- Managing functional safety: Tailoring safety activities, safety culture, confirmation measures, audit and assessment processes.
- Concept phase: Hazard Analysis and Risk Assessment (HARA), assigning safety goals, Automotive Safety Integrity Level (ASIL) ratings, Functional Safety Concept (FSC).
- System-level development: Technical Safety Concept (TSC), system and item integration and testing, safety validation, Hardware-Software Interface (HSI) specification.
- Hardware development: Safety requirements and design, hardware architectural metrics, including types of faults and diagnostic coverage, hardware testing.
- Software development: Safety requirements and design, software architecture, software unit and integration testing, qualification of software components.
- Production, operation, service and decommissioning: Preproduction planning requirements, manufacturing-related functional safety topics, service and user manual guidelines.
- Supporting processes: Criteria for the coexistence of elements, ASIL decomposition, analysis of dependent failures, confidence in software tools.
To sum up, hazards in the automotive industry highlight the need for effective safety training. Using microlearning to supplement safety training can significantly enhance knowledge retention and employee engagement. RapL is a leading provider of microlearning solutions. RapL offers a comprehensive and tailored approach to safety training in the automotive sector. This ultimately ensures a safer and more informed workforce. To know more, contact us at hello@getrapl.com.

Download it now!
Dear reader, thanks for being with us all the way till the end. We suggest 2 things from here
1. Speak to us if you want a microlearning strategy deep-dive: Microlearning is extremely effective, if approached sensibly. Microlearning is the answer to today’s shortening attention spans and we know how to make learning successful via microlearning. Drop your context here and we shall partner with you for the rest.
2. Lap up more content: We have written some intense literature on how microlearning is the superglue between people and successful business operations. Access all of it here.
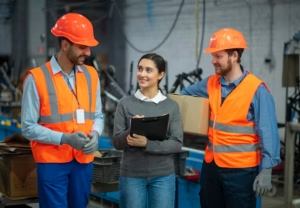
Top Knowledge Retention Strategies for Frontline Teams
In today’s fast-paced operational environments, the efficiency and accuracy of frontline workers can significantly influence an organization’s success…

The Ultimate Guide to Frontline Employee Training
Who Are Frontline Employees? Frontline employees are the face of your business. They are the customer service representatives, field agents, retail staff, warehouse operators, and service technicians who interact directly with customers, products, and operational processes. Their impact on business success is immediate and measurable, as they: ✅ Drive customer satisfaction through direct interactions.✅ Influence revenue generation in sales and service roles.✅ Ensure operational efficiency in logistics and supply chains.✅ Handle safety and compliance, reducing workplace risks. Without proper frontline employee training, organizations risk high turnover, inconsistent service quality, and reduced productivity—leading to costly operational inefficiencies. How Are Frontline Employees Categorized in an Organization? Organizations typically structure frontline employees based on their roles and responsibilities. For instance: Customer-Facing Teams: Retail associates, call center representatives, and sales agents who provide direct customer interactions. Field Teams: Field sales reps, service technicians, and delivery staff working outside the office. Operations and Support: Logistics workers, facility managers, and warehouse operators who ensure seamless internal processes. Different Types of Frontline Employees and Their Activities Customer Service Representatives: Handling customer inquiries and complaints. Providing product recommendations and support. Field Sales and Agents: Engaging customers in their environment. Promoting products and closing deals. Warehouse & Logistics Workers: Managing inventory and supply chain logistics. Ensuring timely deliveries and reducing operational errors. Facility and Maintenance Teams: Maintaining safety and compliance standards. Conducting routine audits and reporting issues. Why Should Frontline Employees Matter to an Organization? Frontline employees are a direct link between the company and its customers. When empowered, they: Enhance customer experiences with improved service and response times. Increase sales conversions by confidently communicating product value. Ensure operational efficiency through optimized workflows. Strengthen brand loyalty by delivering consistent service quality. Why Is Training Needed for Frontline Employees? Many frontline workers operate in high-pressure, fast-paced environments with little time for formal training. Without effective learning opportunities, they: Struggle to keep up with changing processes and new technologies. Lack confidence in customer interactions, leading to lost business. Miss important safety and compliance protocols, increasing risk. Feel disengaged, resulting in higher turnover rates. Why Frontline Employees Hesitate to Engage with Training Despite its benefits, many frontline employees see training as a burden. Common barriers include: ❌ Training sessions feel too long and disrupt daily work schedules.❌ Content is generic and doesn’t address real challenges.❌ Lack of clear incentives or immediate impact on their performance.❌ Limited access to training platforms, especially in field-based roles. The Role of Engaging Content in Frontline employee training Let’s be honest—boring training content gets ignored. RapL Craft makes content creation effortless and engaging: 🎥 AI-powered tool to create interactive, high-quality learning materials in minutes 📚 Create quizzes, tests, assignments, surveys with just simple prompts 🎮 Integrate learning content creation into your workflows, save time and improve efficiency With RapL Craft, businesses can quickly develop impactful training content that resonates with employees and keeps them engaged. Explore Craft today! Best Practices for Frontline Employee Training: Making Learning Stick The best frontline employee training programs blend different learning methods for maximum engagement and retention. Here’s how: 🎯 On-the-Job Learning: Employees learn best by doing! Pairing hands-on experience with structured training creates a stronger learning experience. 📱 Mobile & Microlearning: Short, engaging modules fit into busy schedules and ensure knowledge is absorbed in bite-sized pieces. 🏆 Gamification & Rewards: Who doesn’t love a little competition? Adding leaderboards, challenges, and rewards makes training fun and engaging. 📊 KPI-Based Learning: Training must connect to employee performance metrics so workers see its relevance and impact. 🔄 Continuous Learning & Reinforcement: One-time training sessions won’t cut it—regular knowledge reinforcement is key to long-term success. How to Measure Training Effectiveness: Linking Training to KPIs A frontline employee training program should directly impact business metrics. Here’s what to track: 📈 Performance Improvement: Are employees hitting their sales, service, or operational KPIs post-training? ✅ Training Completion & Engagement Rates: Are employees actively participating and completing training modules? 📊 Knowledge Retention: Are employees applying what they’ve learned on the job? 🙌 Customer & Employee Feedback: Are customers and frontline workers noticing the benefits of training? Tracking these indicators ensures training is not just a one-off event but a measurable driver of business success. The Role of Knowledge Mapping & Analytics Data-driven decision-making is essential for frontline employee training success. RapL Analytics helps companies: 🔍 Identify knowledge gaps of the frontline employees through real-time performance tracking and learning engagement 📊 Monitor training impact on key KPIs, correlate training to the individual KPIs of employees and measure the impact in real time 📈 Enable managers to fine-tune training programs based on data and provide regular feedback to nudge frontline employees to perform better By leveraging RapL Analytics, businesses ensure frontline employees receive relevant, impactful training that leads to measurable performance improvements. Key Takeaways: Future-Proofing Your Frontline Employees 🚀 Frontline training isn’t optional—it’s a business game-changer. Well-trained employees mean better customer experiences, improved safety, and higher productivity. 📱 Modern training needs to be digital-first. Mobile learning, microlearning, and interactive methods keep frontline employees engaged. 🏆 Mix it up! The best training programs combine gamification, real-time coaching, and data-driven insights for lasting impact. 📊 Measure everything. Link training to performance KPIs, customer satisfaction, and employee retention for real ROI. 💡 Leverage AI & automation. RapL Analytics, and Craft take the hassle out of training, making it smarter, faster, and more effective. Empower your frontline teams. Strengthen your business. Let’s make frontline training work.

The Ultimate Guide to Customized Employee Training: Strategies, Benefits, and Best Practices
Traditional, one-size-fits-all training programs often fail to address the specific needs of employees. Every job role requires distinct skills, and employees..

Top 15 training and learning metrics that drive business growth and ROI
Training and learning metrics are measurable indicators used to evaluate the effectiveness, efficiency, and outcomes of employee training programs…

Download it now!